

CASE
STUDIES
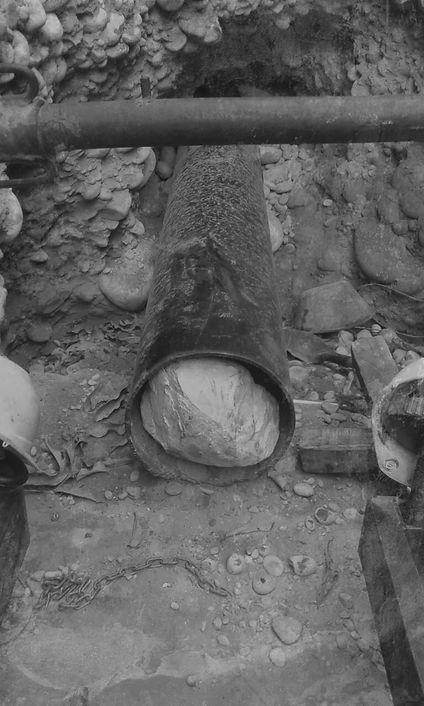
Working under tough ground conditions
Project Specifications
Length: 2 Drives, 75 ft each. (Total 150 ft)
Diameters: 16” and 30”
Type of Soil: High Density of Cobblestone
The presence of cobblestone and boulders in the terrain made it very difficult for other trenchless technologies to execute this project.
The project was designed for a conventional 12” Pipe Rammer. However, unexpected boulders forced the suspension of the project after installing 6ft of the 16" metal casing. With a small scale of our current machine, we were capable of installing the full two drives on both diameters. All of it, at a fraction of the cost of competing options.
This project served as an important milestone for our company because it proved the science underlying our technology and secured many other projects in the region.
The picture shows some of the boulders that we broke.
Where others were too expensive
Project Specifications
Length: 400 meters across 5 drives (1310 ft) - Maximum drive: 280ft @ 36"
Diameters: 30”, 36” and 42”
Type of Soil: Cohesive Clay + Water
This project was originally designed for open-cut. However, the unstable soil and installation depth made the project non-viable. As a result, the project owner required a trenchless machine capable of installing three different pipe diameters under a very unstable soil. That variety of diameters, lengths and complex ground conditions made the project cost prohibiting when using other technologies.
The versatility of our patented technology made us the most cost-effective alternative for our partner. Zilper's quote provided 58% cost savings versus competing alternatives.
Thanks to our tech and support, our customer successfully installed 400 meters (1310 ft) of pipeline despite the challenging conditions.
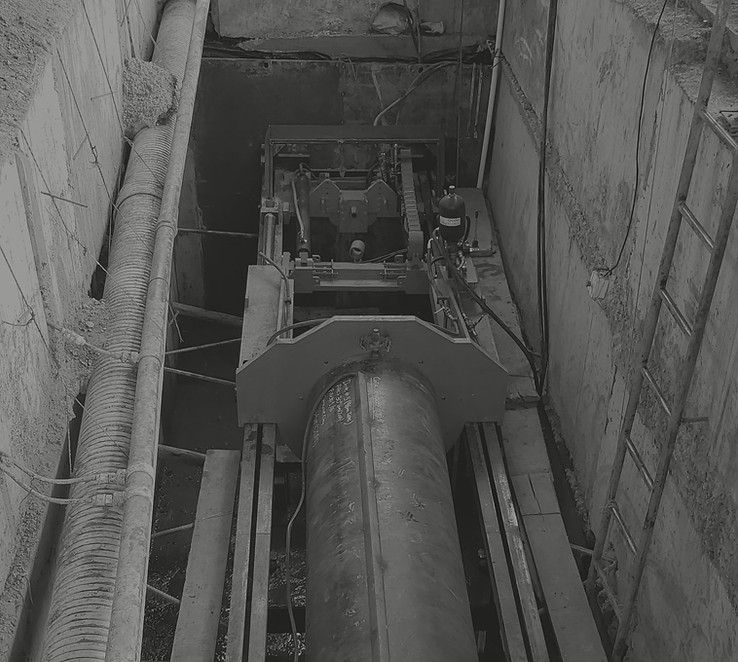
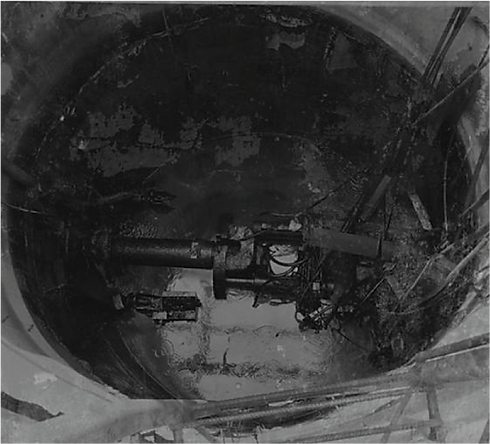
Where others failed
Project Specifications
Length: 50 meters (164ft)
Diameters: 44"”
Type of Soil: Sand + Boulders + Water
The soil conditions in this project were very complex. The terrain was sandy, unstable, watery with cobblestones and boulders. Despite the complicated terrain, other contractors tried executing the project with a conventional Auger Boring and a Guided Boring Machine. In both cases, the machines generated surface undercuts (sinkholes) and had to abandon the project.
​
Furthermore, the boulders got the GBM so stuck that the machine broke a hydraulic jack while trying to unstick its augers (see picture).
Our partner, with our guidance, used Zilper's machine to install a 44" casing to finish the project and recover the augers left by the GBM.